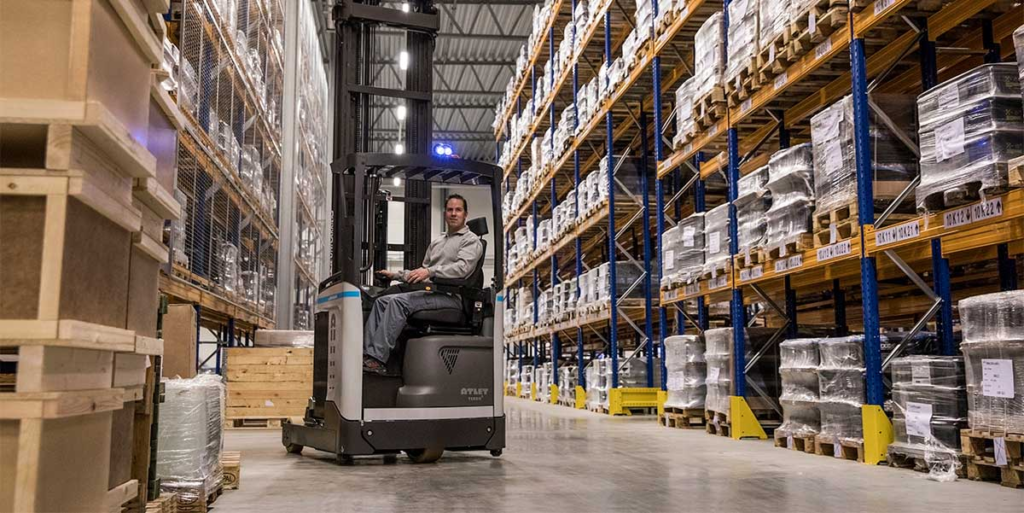
Warehouse flooring is the unsung hero of any logistics or storage operation. It endures the weight of heavy pallets, the constant movement of forklifts, and the daily grind of workers—all while keeping your business running smoothly. However, without proper care, even the toughest floors can deteriorate, leading to costly repairs and operational setbacks. Here’s a practical guide on how to look after your industrial flooring UK and keep it in top shape for years to come.
1. Start with Regular Cleaning
Dust, dirt, and debris are more than just eyesores—they’re silent destroyers of warehouse floors. Over time, grit can scratch surfaces, while spills can erode coatings or seep into cracks. Establish a routine cleaning schedule to prevent buildup:
Sweep Daily:
Use a stiff-bristled broom or an industrial floor sweeper to remove loose particles.
Mop Weekly:
For sealed or coated floors (like epoxy or polyurethane), use a mild detergent and water to tackle stains. Avoid harsh chemicals that could damage the finish.
Address Spills Immediately:
Oil, grease, or chemical spills should be cleaned up promptly to prevent staining or weakening the floor’s integrity.
A clean floor not only lasts longer but also reduces slip hazards for your team.
2. Inspect and Repair Damage Early
Warehouse floors take a beating, and small issues—like cracks, chips, or worn patches—can quickly escalate if ignored. Make it a habit to inspect your flooring regularly:
Look for Warning Signs:
Cracks, uneven spots, or areas where the coating is peeling.
Act Fast:
For minor damage, use a quick-setting filler or patch kit compatible with your flooring type (e.g., concrete repair compounds). For larger issues, call in a professional to prevent further deterioration.
Check Drainage:
Poor drainage can lead to water pooling, which weakens concrete over time. Ensure drains are clear and functioning.
Early intervention saves money and downtime compared to replacing an entire section later.
3. Protect High-Traffic Zones
Not all parts of your warehouse see the same wear. Forklift lanes, loading bays, and picking areas endure the most stress. To extend the life of your flooring:
Use Mats or Pads:
Place heavy-duty rubber mats in high-impact zones to absorb shock from dropped items or heavy equipment.
Maintain Equipment:
Ensure forklifts have smooth, non-abrasive tires and avoid overloading them, which can gouge or crack the floor.
Apply Sealants:
For concrete floors, a fresh layer of sealant every few years adds an extra shield against wear and tear.
Protecting these hotspots keeps your entire floor performing at its best.
4. Control Moisture and Temperature
Warehouses can be harsh environments, especially in climates prone to dampness or temperature swings. Excess moisture weakens concrete and promotes mold, while extreme heat or cold can cause expansion and cracking. Here’s how to manage it:
Ventilate Properly:
Use fans or dehumidifiers to keep air circulating and reduce humidity.
Monitor Leaks:
Fix roof leaks or plumbing issues that could expose the floor to water.
Choose the Right Coating:
If your floor isn’t already sealed, consider a moisture-resistant coating tailored to your warehouse’s needs.
A stable environment prevents premature aging of your flooring.
5. Train Your Team
Your employees play a big role in floor maintenance, whether they realize it or not. Equip them with the knowledge to help:
Spill Reporting:
Encourage immediate reporting and cleanup of spills.
Equipment Handling:
Train forklift operators to avoid sharp turns or sudden stops that can scuff or dent the floor.
Footwear Rules:
In dusty or dirty warehouses, enforce boot cleaning to prevent abrasive particles from being tracked in.
A well-informed team becomes your first line of defense against floor damage.
6. Schedule Professional Maintenance
Even with diligent care, warehouse flooring benefits from expert attention. Every 12–18 months (depending on usage), hire a professional to:
Deep Clean:
Industrial-grade equipment can remove ingrained dirt that daily cleaning misses.
Reapply Coatings:
Refresh sealants or topcoats to restore protection and shine.
Assess Structural Health:
Experts can spot underlying issues, like subfloor weaknesses, that you might overlook.
Think of it as a tune-up to keep your floor in peak condition.
Conclusion: A Little Care Goes a Long Way
Your warehouse floor is an investment worth protecting. By cleaning regularly, repairing damage promptly, and taking preventative steps, you can extend its lifespan and avoid the headache of premature replacements. A well-maintained floor doesn’t just save money—it keeps your warehouse safe, efficient, and ready for business every day.
Need help getting started? Reach out to a flooring specialist to assess your warehouse and create a maintenance plan tailored to your operation.